Home > Company News > Automotive parts injection molding processing surface replication bad how to do?
Company News
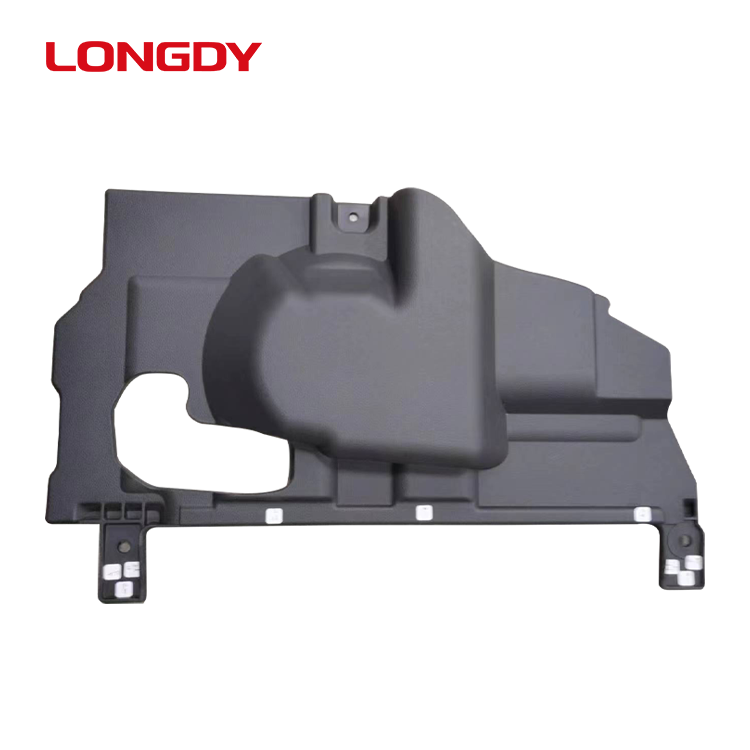
Poor surface replication is a common problem in automotive parts injection molding during processing. This will lead to a decline in the quality of product appearance, and even affect the function and performance of the product. The following will introduce the causes, solutions and preventive measures for poor surface replication of automotive parts injection molding processing in detail.
First, automotive parts injection molding processing surface reproduction of the reasons for bad
1. unreasonable mold design: mold is the basis of injection molding parts processing, if the mold design is unreasonable, such as improper selection of parting surface, exhaust system design is unreasonable, etc., may lead to poor surface replication.
2. injection molding material problems: injection molding material fluidity, shrinkage and other parameters are not appropriate, or the material contains impurities, moisture, etc., may lead to poor surface reproduction.
3. improperly set injection molding process parameters: injection molding process parameters including temperature, pressure, speed, etc., if not properly set, may lead to unstable flow of plastic melt in the mold, thus affecting the surface replication effect.
4. Equipment problems: the stability and precision of the injection molding machine will affect the surface reproduction effect. If the equipment is aging and badly worn, it may lead to poor surface reproduction.
5. Inadequate operator skills: the operator's understanding of the injection molding process, operating skills, etc. will affect the surface reproduction effect. If the operator's skills are insufficient, it may lead to poor surface reproduction.
Second, automotive parts injection molding processing surface replication of bad solutions
1. Optimization of mold design: For the problem of unreasonable mold design, it can be solved by improving the selection of parting surface and optimizing the design of exhaust system, etc. At the same time, it can also be solved by computer-aided design. At the same time, you can also use computer-aided design (CAD) technology to improve the accuracy and efficiency of mold design.
2. Strictly control the quality of injection molding materials: choose suitable injection molding materials to ensure that their fluidity, shrinkage and other parameters meet the requirements. At the same time, the material should be strictly inspected to ensure that it does not contain impurities, moisture and so on.
3. Adjust the injection molding process parameters: According to the actual production situation, set the temperature, pressure, speed and other process parameters reasonably to ensure the stable flow of plastic melt in the mold. At the same time, the state of the equipment should be checked regularly to ensure the normal operation of the equipment.
4. Improve operator skills: Strengthen the training of operators to improve their understanding of the injection molding process and operation skills. At the same time, it is necessary to establish a perfect quality management system to analyze and deal with the problems arising in the production process in a timely manner.
Third, automotive parts injection molding processing surface replication of poor preventive measures
1. Strengthen the quality control of the mold design stage: in the mold design stage, we should fully consider the structural characteristics of the product, molding process and other factors to ensure the reasonableness and feasibility of the mold design.
2. Strictly control the quality of injection molding materials: choose high-quality injection molding materials, strengthen the inspection and acceptance of materials to ensure that the quality of materials meet the requirements.
3. Regular maintenance of equipment: regular maintenance and maintenance of injection molding machines to ensure the normal operation and stability of the equipment.
At the same time, pay attention to the renewal of equipment, improve the precision and performance of the equipment.
4. Establish perfect quality management system: establish perfect quality management system, strictly monitor and manage the key links in the production process to ensure the stability and reliability of product quality.