Home > Company News > Uncover the problem of blocking hole in stamping processing, a move to easily solve!
Company News
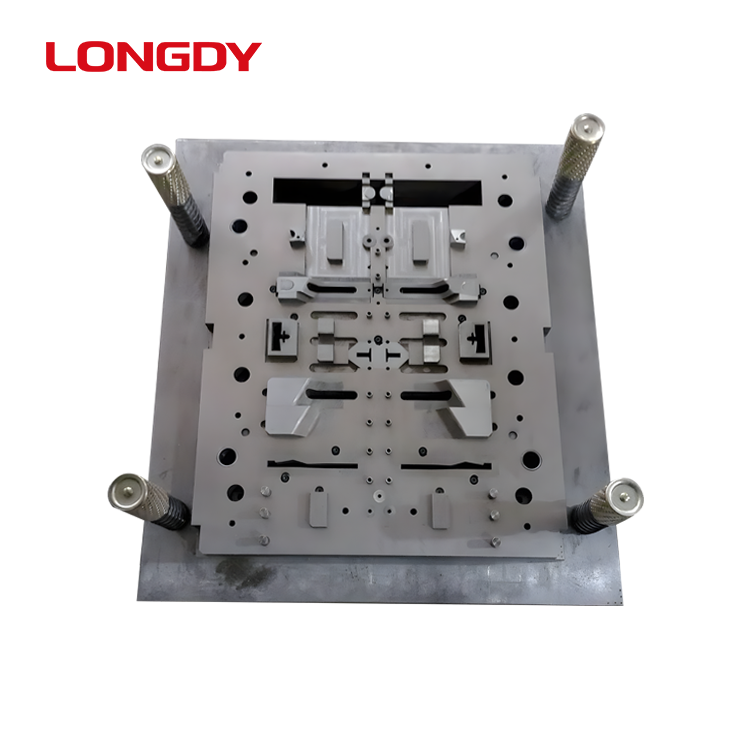
In the field of metal hardware stamping processing, the treatment of scrap has always been a key link to improve efficiency and ensure smooth production. Scrap blocking hole problem, not only affects the production efficiency, but also may lead to mold damage, increase production costs. Therefore, to effectively solve this problem for the production enterprises is crucial.
First of all, we need to understand the causes of scrap blocking hole in stamping processing.
Often, this may be related to the punch length is not enough, the die clearance is too large, as well as magnetic problems. Taking appropriate measures to address these issues is key. For example, when the length of the punch is not enough, it can be solved by replacing the punch and ensuring that the edge of the new punch cuts into the concave die a material thickness plus 1mm; if the concave die clearance is too large, the situation can be improved by reducing the die clearance; if the punch or template is magnetic, the use of demagnetizers to demagnetize the process is also an effective solution.
In addition to the common causes mentioned above, the problem of scrap plugging hole in stamping processing may also be caused by improper design of the drop hole.
For example, the drop hole is too small or the position is offset, will lead to drop material is not smooth, then should consider increasing the drop hole and adjust its position to improve the situation.
In addition, the knife mouth design is also an important factor affecting the discharge of waste.
If the knife mouth is not put taper, you can consider wire cutting taper or reverse expansion to reduce the length of the straight wall bit; knife mouth straight wall bit is too long, through the reverse drilling way to make the knife mouth straight wall bit shortened, so as to avoid the waste material clogging.
In addition, edge chipping caused by large burrs can also cause blockage, which requires regrinding the edge to solve the problem.
It is worth mentioning that improper use of shims during stamping processing may also be one of the causes of scrap plugging.
In this case, the number of shims should be minimized and steel shims should be used to ensure that the shims are correctly set under the die.
Solving the problem of scrap plugging in stamping processing is a systematic project, involving mold design, material selection, processing technology and other aspects. Manufacturers need to apply the above measures flexibly according to their own actual situation, and continuously optimize the process parameters in order to achieve the best production results. At the same time, regular maintenance and inspection is also an effective means of preventing and solving the waste problem to ensure the efficient and stable operation of the stamping production line.