Home > Company News > Stamping Mold Design Key Points
Company News
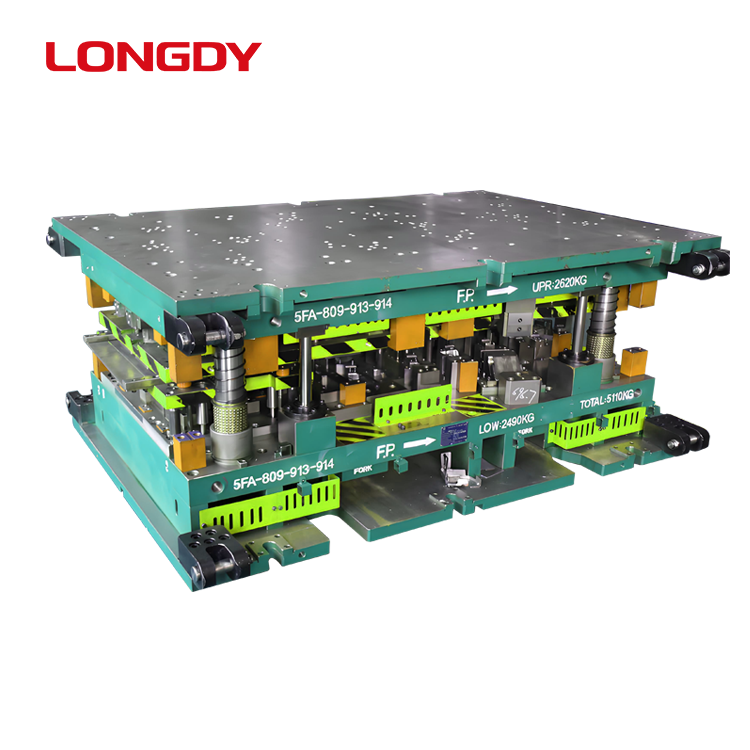
Stamping die design plays a key role in modern manufacturing. It is like a precision artist, molding sheet metal into a variety of useful parts and components through accurate calculations and meticulous processes. In this article, we'll take a closer look at the nuts and bolts of stamping die design.
Stamping die design involves many aspects, from material selection to die structure design, each step needs to be carefully designed to ensure the accuracy and reliability of the final product.
First, choosing the right material is critical.
The hardness, toughness and heat resistance of the material directly affect the performance and life of the mold. For example, high carbon and alloy steels are often used to produce durable stamping dies due to their excellent hardness and wear resistance.
The choice of die type is also a critical step in the design process.
Single-engineered, composite and progressive dies are the three most common types, each with different application scenarios based on production needs and complexity. Single-engineered molds are suitable for rapid production of simple shapes, while progressive molds can handle more complex multi-step production processes.
Accurate calculations are indispensable in mold design.
Designers need to calculate the punching force, the way the pattern is lined up, and the size of the cutting edges, which are parameters that determine whether the mold will perform its task accurately and efficiently. For example, the calculation of press force involves factors such as material thickness, hardness and the required molding depth. Correct calculations ensure that the metal flows evenly during the stamping process, avoiding breakage or deformation.
The guiding and positioning systems of the mold are also critical aspects of the design.
The guiding system ensures the accuracy and stability of the mold in high-speed movement, while the positioning system ensures precise alignment for every stamping, which is critical for consistency and quality in mass production. The designer must consider the overall layout of the mold and the synergy of the various components.