What are the measures to reduce material loss in injection molding processing?
2024-04-24 18:02:38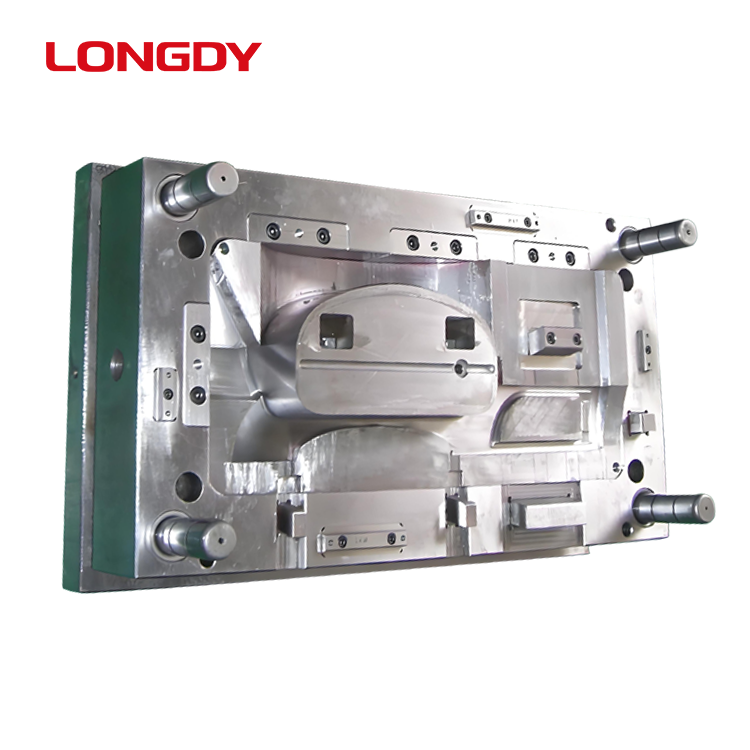
Reducing material loss in the production process of injection molding not only saves costs, but also contributes to environmental protection.
In the injection molding process, material loss is mainly reflected in several aspects: unnecessary consumption of raw materials, the scrap rate of the molding process, and the trimmings in the post-processing. For these loss points, you can take appropriate measures to reduce the loss.
1. Unnecessary consumption of raw materials for injection molding process. In order to ensure the quality and precision of injection molded products, raw materials are usually preheated and dried. In this process, if the temperature is not properly controlled or the time is too long, it may lead to a decline in raw material performance or even degradation, resulting in unnecessary material losses. Therefore, optimizing the temperature control system and adjusting the appropriate preheating temperature and time according to the characteristics of different materials are the key steps to reduce the loss of raw materials.
2. Reasonable design of mold is also an important means to reduce material loss. The design of the mold is not only related to the quality of the product, but also directly affects the efficiency of material use. By adopting high-efficiency cooling system and heating system, the molding cycle can be shortened and the production efficiency can be improved. At the same time, optimize the mold runner design, so that the molten plastic can fill the mold cavity more quickly and evenly, reducing the waste of material in the runner.
3. Next focus on the scrap rate of injection molding process. There are many factors affecting the scrap rate, including the stability of the machine, the skills of the operator, and the setting of process parameters. Improve the stability and accuracy of the equipment, regular maintenance of the equipment, can reduce production interruptions caused by equipment failure and defective products. In the setting of process parameters, by precisely controlling the injection pressure, injection speed, holding time and cooling time, etc., we can ensure the quality of the product and reduce the rejects caused by improper parameters.
4. As for the problem of trimmings in post-processing, it is usually possible to reduce the loss by recycling. The establishment of a perfect edge material recycling system, will produce the edge material for classification, crushing, re-granulation, and put into production use again, not only reduces the waste of materials, but also reduces the cost of production.
5. The implementation of lean production management of injection molding processing is also an effective strategy to reduce material loss. Through continuous improvement of the production process, eliminate waste and achieve production optimization. This includes the standardization of the production process, the refinement of the production plan and the real-time monitoring of material flow.