Home > Company News > What are the main components of injection molds
Company News
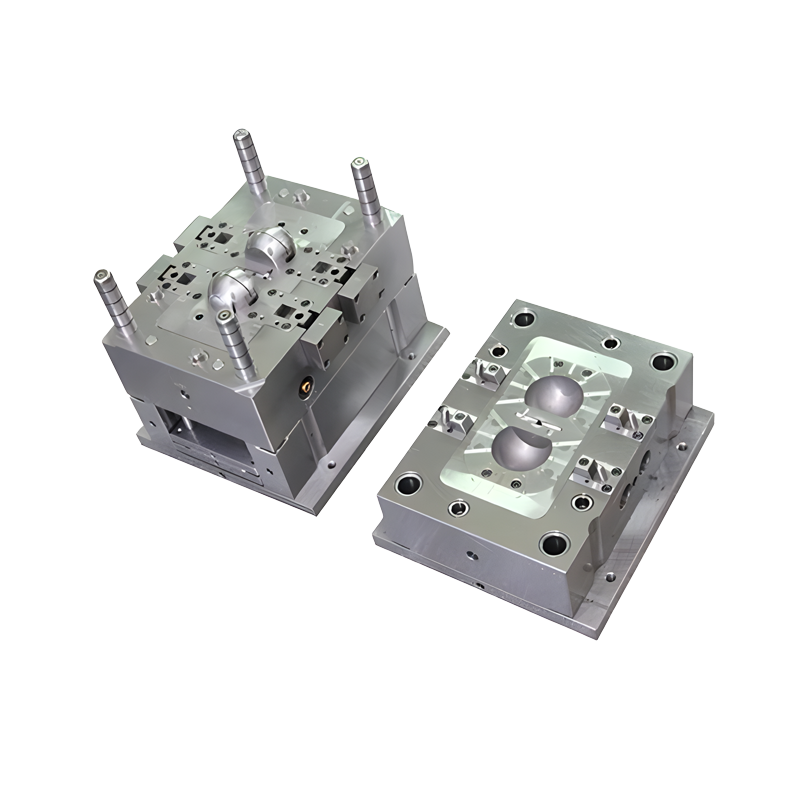
The production of plastic products requires the use of injection molds, which are composed of multiple main parts. Firstly, the main body of the mold is made of durable steel to ensure that it can withstand the high-pressure injection molding process. The structure of the mold body fully considers the characteristics and processing requirements of plastic materials to achieve the best injection molding effect. Secondly, the cavity and core of the mold are indispensable parts in the injection molding process. Their shape and size determine the appearance and size of the final plastic product. In order to ensure the lifespan of the mold and the accuracy of the plastic parts, the mold cavity and core need to undergo precision machining. According to specific injection molding requirements, the mold cavity and core can be fixed or detachable.
In injection molds, in addition to the cavity and core, there are other auxiliary components. For example, the role of the guiding mechanism is to ensure smooth and accurate movement of the mold during opening and closing. Usually, the guide mechanism consists of a guide pillar and a guide sleeve, whose function is similar to a guide rail to prevent mold displacement or damage during the injection molding process. The cooling system is also an important component used to control the temperature of the mold to ensure that plastic materials can quickly solidify and maintain shape. Generally speaking, a cooling system consists of cooling water pipes or channels, which absorb and dissipate heat by circulating the coolant.
In injection molds, there is also a mold opening device specifically designed to assist in releasing plastic products and prevent them from getting stuck in the mold and unable to be removed. The mold opening device can be mechanically operated, such as using an ejector pin or an inclined ejector mechanism, or pneumatically operated, such as using a pneumatic release system. When selecting and designing the mold opening device, it is necessary to ensure that it can open and close smoothly without causing any damage to the product itself.
Ultimately, injection molds typically consist of components such as guide plates, support columns, and templates. The guide plate fixes and guides the mold cavity and core, and the support column is used to bear the weight of the mold and provide stability during mold opening and closing. The template connects all components and provides support for the overall structure.
According to the above, the injection mold is composed of the mold body, mold cavity and core, guide mechanism, cooling system, mold opening device, guide plate, support column, and template. These components work closely together to ensure the smooth injection molding process and produce high-quality plastic products. When designing and manufacturing molds, it is necessary to consider factors such as material strength, wear resistance, and thermal conductivity, as well as the shape and size requirements of injection molded products, to meet customer needs. At the same time, precision machining and quality control are also very important links to ensure product quality and stability.